Welding inverter circuit. The schematic diagram of the welding inverter
The article will consider the classical schemewelding inverter. To date, they are very popular, the price is quite affordable. They have a lot of positive qualities, in particular, the simplicity of work and light weight. But, like other electronic devices, the welding machine can fail. And in order to carry out qualitative repairs, it is necessary at least in general terms to have an idea of its device, from which elements the inverter circuit consists. Without this, you can not repair the welders, in the circuit of which inverter converters are used. Therefore, it is necessary to learn a lot about the theory of this device.
Basic information about inverter units

In fact, this power supply unit, the principle of its operationsimilar to the one used in personal computers. The transformation of electrical energy takes place according to the same principles, in spite of the fact that the sizes and functions of these devices are different. There are several stages that can be identified in the welding inverter. The first thing is to convert the AC voltage, which comes from the 220 V network, to a constant. About how this happens, will be told a little lower, as well as the electrical diagram of the welding inverter.
Then this voltage is convertedin variable, but with a higher frequency. You know that the frequency of the current in the electrical network is 50 Hz. Inverter welding machines there is an increase of up to 80 thousand Hz. Then it is necessary to reduce the voltage value with a high frequency. At the last stage, this low voltage transforms at a frequency of about 80,000 Hz. This is a brief description, in fact, all stages can be broken down into smaller parts. But to understand the principle of functioning this is enough.
Due to what the weight of the welding apparatus decreases

And now about why the schemes were choseninverter type. Look at the welding machines that were used before, including homemade ones. Their main purpose is to reduce the AC voltage, which comes from the household electricity network to a safe value, but with a large secondary current. For this reason, the primary winding is wound with a thinner wire than the secondary winding. The thickness of the wire determines what current you get in the winding. Below is a schematic diagram of the welding inverter in the article. Carefully study it to have an idea of what elements are included in it. For welding, several hundred amperes are sometimes necessary. Due to the fact that the power of such transformers is very high, and they work only at a frequency of 50 Hz, in addition, they have very large dimensions. As you understand, the frequency of the incoming and outgoing current is the same. In other words, if you applied 50 Hz to the primary winding, remove the electric current from the secondary with the same parameters.
Operating frequency of the inverter

But thanks to inverter welding machines,in which the operating frequency is increased by a value of the order of eighty thousand hertz, and in some devices even more, it is possible many times to reduce the dimensions of the transformers that are used in the conversion of electric current. If you increase the operating frequency, you can reduce the transformer at least four times. Consequently, the total weight of the entire welder will be very small. The cost of this device is also reduced, as there is a saving in copper and steel, which are used in the manufacture of transformers. But in order to obtain such a frequency value, it is necessary to use inverter circuits. They consist of powerful field effect transistors that operate in key mode. With their help, the current is switched with the frequency necessary for operation. Please note that the field-effect transistor can only work at a constant voltage. It is worth noting that the scheme of the welding inverter "Resanta" in many respects similar to the one used in other devices.
Principle of operation of the rectifier
Therefore, before you give them food,it is necessary to rectify the incoming current. For this, a rectifier is used, in which there are powerful diodes. They are connected by a bridge circuit. After this, the variable component is cut off by electrolytic capacitors. This occurs at the first stage of the transformation. Field-effect transistors are connected to the transformer. With it, you can reduce the voltage. As mentioned above, these transistors produce current switching with a frequency of sometimes even more than 80,000 Hz. It is clear that the transformer must also be designed to work with such parameters. The dimensions of this device are very small, it can not be compared with those used in conventional transformer welding machines. But his power is the same. It is clear that there are many more elements that are necessary for the stable operation of the welding machine. And now more in detail about how each unit of a conventional welding inverter works. It has two main parts - the power and control circuit.
Rectifier cascade

In this block there is a transformationAC, which comes from the network of 220 volts. It has several semiconductor diodes with high power, as well as electrolytic capacitors and a choke. This results in the fact that alternating current with an operating frequency of 50 Hz becomes constant. Condensers are necessary to cut off the variable component, which still remains in the rectified voltage. Note that there are several variants of circuits for rectifying the voltage. If the connection is to be made to a three-phase network, the circuit of the semiconductor diodes will be slightly different. Therefore, you need to decide what you need a welding inverter circuit. With your hands, such a device can be assembled quite simply.
Filters
Note also that almostthe voltage is increased by one and a half times after it reaches the filter collected on the electrolytic capacitors. In other words, if the mains is 220V, then on the terminals of the capacitors, if you measure it, there will be 310V. To smooth the current pulsations, in order to avoid high-frequency interference, and to avoid getting into the power grid, a special filter must be installed. Usually it is assembled on a throttle, which is wound on an annular core, and several capacitors are also included in the circuit.
Inverter cascade

Typically, twopowerful transistors that work in key mode. It should be noted that they are necessarily mounted on an aluminum radiator. There is also an additional forced cooling with a fan. Due to these transistors there is a commutation of the DC voltage, which is then fed to the pulse transformer. Moreover, switching occurs at a frequency of about 80 kHz. But there is a difference from the alternating current that flows in the household electrical system. First, the very value of the frequency is many times greater than it. Secondly, the shape of the pulse of this alternating voltage, which is produced by the field-effect transistors, is rectangular, and not a sine wave. To protect transistors from excessive overvoltage, it is necessary to use a circuit consisting of resistors and capacitors. It is worth noting that the basic electrical scheme of the welding inverter does not do without these elements.
HF Transformer
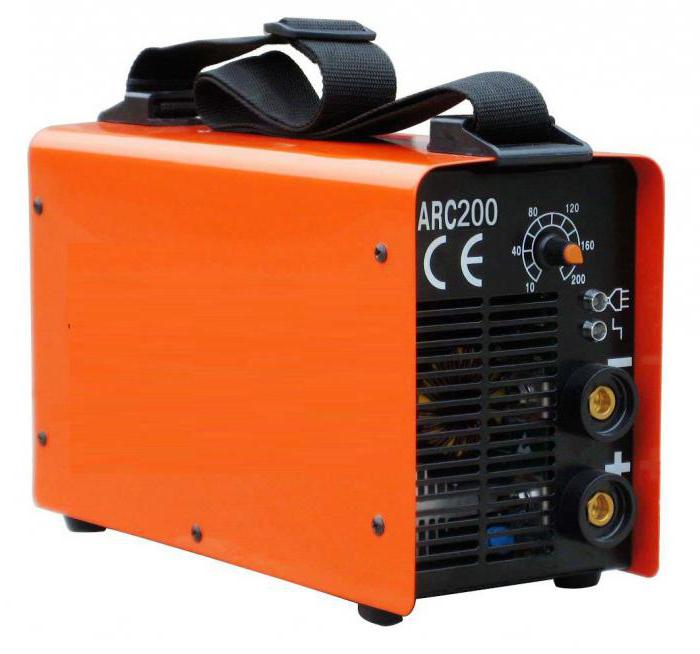
High-frequency transformer, for whichvoltage from the transistors working in the key mode, allows you to reduce its value to 65 volts on average. But at the same time the current can be about 130 A. You can even draw an analogy with the ignition coil, which is used in cars. In welding inverters, a high voltage is applied to the primary winding, but the current is very small. The voltage from the secondary winding is removed with a lower value, but the current is increased. Please note that the car ignition coil works in the opposite way. That is, a low voltage with a high current is applied to the primary winding. And with the secondary, a high voltage is removed, but with a lower current value.
Output Rectifier

But it's worth looking at what componentsis also el. Welding inverter circuit. The output is also equipped with a rectifier, which is assembled from high-power semiconductor diodes. They have a very high speed, they open and close in a time that is much less than 50 nanoseconds. Note when designing welding inverters that it is necessary to select these semiconductor elements in such a way that their parameters satisfy the operating mode. Simple diodes can not cope with the task, because they can not open and close in a timely manner. Immediately excessive heating will begin and, as a result, failure. For this reason, it is necessary to install diodes that have very short switching times during design or during repair.